Anhui Feichun Special Cable Co.,Ltd Li.wang@feichuncables.com
What Are the Key SANS Standards for Hoists and Lifting Equipment in South African Mines?
Discover the critical South African National Standards (SANS) for hoists and lifting equipment in South African mines, ensuring safety, reliability, and compliance in harsh mining environments. Learn how these standards reduce accidents and improve operational efficiency.
Li.wang@Feichun Cable
7/8/20257 min read
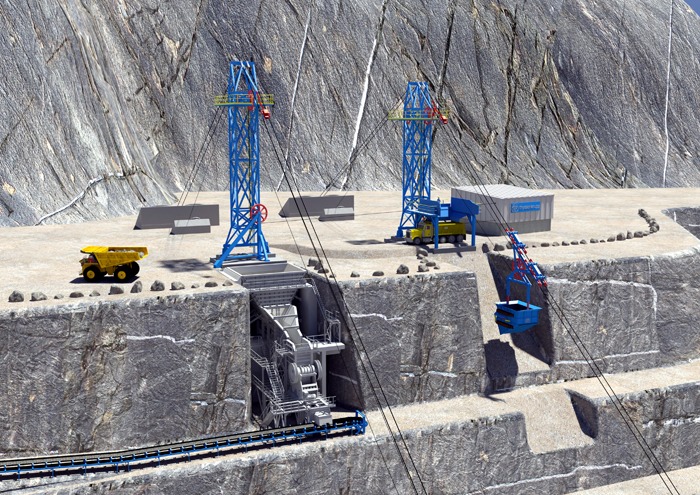
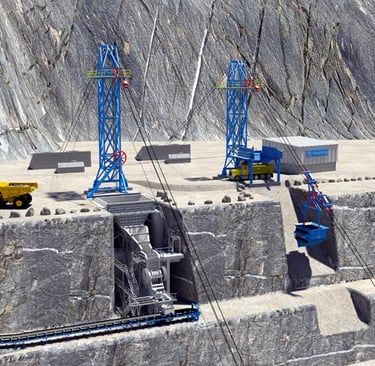
Mining is the backbone of South Africa’s economy, but it comes with significant risks. The harsh underground conditions—think dust, heat, and heavy loads—put immense pressure on equipment like hoists and lifting gear. A single failure can lead to catastrophic accidents, endangering lives and halting operations. This is where South African National Standards (SANS), set by the South African Bureau of Standards (SABS), come in. These standards provide strict guidelines to ensure that hoists, cranes, and other lifting equipment used in mines are safe, reliable, and fit for purpose. But what exactly are these standards, and why should miners, engineers, and mine managers care? This article dives into the key SANS standards for hoists and lifting equipment in South African mines, exploring their importance, benefits, and impact on the industry. By the end, you’ll understand how SANS compliance keeps mines running smoothly and workers safe.
What Are SANS Standards?
SANS, or South African National Standards, are a set of technical specifications developed by the South African Bureau of Standards (SABS), a statutory body responsible for promoting quality and safety across industries. In the context of mining, SANS standards are not just recommendations—they’re often legally binding under the Mine Health and Safety Act No. 29 of 1996. These standards cover everything from the design and construction of equipment to its maintenance and inspection, ensuring that every piece of machinery can withstand the punishing conditions of a mine.
For hoists and lifting equipment, SANS standards focus on critical components like wire ropes, chains, hooks, and lifts. They set out precise requirements for materials, manufacturing processes, and performance testing to prevent failures that could lead to accidents. Compliance with SANS is enforced through regular inspections by competent persons or registered Lifting Machinery Inspectors (LMIs), as mandated by the Driven Machinery Regulations (DMR) under the Act. For South Africans, these standards are a guarantee that the equipment used in mines meets global best practices, tailored to local conditions.
Why does this matter? In a country where mining employs over 400,000 people and contributes significantly to GDP, ensuring equipment safety is non-negotiable. SANS standards provide a framework that mine operators can rely on to protect workers, reduce downtime, and meet regulatory requirements. Let’s explore the specific standards that govern hoists and lifting equipment in South African mines.
SANS Standards for Hoists and Lifting Equipment
The SANS standards for hoists and lifting equipment in South African mines are comprehensive, addressing every aspect of design, operation, and maintenance. Below are the most critical standards, each tailored to ensure safety and performance in the demanding mining environment.
SANS 1592: Short-Link Steel Chain (Close-Tolerance) for Lifting Appliances
This standard specifies requirements for close-tolerance short-link steel chains used in lifting appliances, such as hoists and slings. These chains are designed to handle heavy loads in mines, where precision and strength are critical. SANS 1592 ensures that chains meet strict tolerances for link dimensions and material strength, reducing the risk of stretching or snapping under load. In mines, where chains are used to lift heavy equipment or transport materials, compliance with this standard is essential to prevent accidents.
SANS 189: Short-Link Steel Chain (Medium-Tolerance) for Lifting Purposes
Unlike SANS 1592, SANS 189 covers medium-tolerance chains, which are used in less precision-critical lifting applications. These chains are still robust enough for mining but allow for slightly looser tolerances, making them cost-effective for general-purpose lifting. This standard ensures that even less specialized chains meet safety requirements, reducing the risk of failure in auxiliary lifting tasks.
SANS 1594: Manually Operated Chain Blocks
Chain blocks are a staple in mining for lifting heavy loads manually. SANS 1594 outlines the design, construction, and testing requirements for these devices, ensuring they can operate safely under high loads. The standard mandates regular inspections (every three months, as per DMR) to check for wear, corrosion, or mechanical defects. For miners working in confined spaces, SANS 1594-compliant chain blocks provide reliable lifting with minimal risk.
SANS 1636: Manually Operated Chain Lever Hoists
Similar to chain blocks, chain lever hoists are used for manual lifting in tight spaces. SANS 1636 sets out requirements for their design and performance, ensuring they can handle the rugged conditions of a mine. These hoists are often used for maintenance tasks, such as lifting machinery components, and must be inspected regularly to maintain safety.
SANS 2408: Steel Wire Ropes for General Purposes
Wire ropes are the lifeline of many mining hoists and cranes. SANS 2408 specifies the construction, testing, and performance of steel wire ropes, ensuring they can withstand the mechanical stress and abrasive conditions of mining. The standard covers rope diameter, tensile strength, and fatigue resistance, with clear guidelines for discarding ropes showing signs of wear, such as broken wires or corrosion.
SANS 4308: Selection of Wire Ropes for Cranes
Building on SANS 2408, SANS 4308 provides guidelines for selecting the right wire ropes for crane applications in mines. It considers factors like load capacity, rope construction, and environmental conditions, ensuring that cranes operate safely and efficiently. This standard is critical for mine managers choosing equipment for heavy-duty lifting tasks.
SANS ISO 4309: Cranes – Wire Ropes – Care and Maintenance, Inspection, and Discard
This standard outlines procedures for inspecting and maintaining wire ropes used in cranes. It specifies criteria for discarding ropes that show excessive wear, corrosion, or broken strands, which is crucial in preventing catastrophic failures. In South African mines, where cranes are used to lift heavy loads in dusty and humid conditions, SANS ISO 4309 ensures that ropes remain safe throughout their service life.
SANS 1595: Forged Steel Lifting Hooks
Lifting hooks are a critical component of hoists and slings. SANS 1595 sets requirements for forged steel hooks, ensuring they can handle heavy loads without deforming or breaking. The standard specifies material quality, design, and testing procedures, making it essential for safe load handling in mines.
SANS ISO 8539: Forged Steel Lifting Components
This standard covers a range of forged steel components, such as shackles and hooks, used in lifting systems. It ensures that all components meet strict safety and performance criteria, reducing the risk of failure during lifting operations. In mines, where components are subject to constant wear, SANS ISO 8539 is vital for maintaining system integrity.
SANS 0019: Inspection, Test, and Examination of Mobile Cranes
Mobile cranes are widely used in mining for material handling and equipment installation. SANS 0019 outlines procedures for inspecting and testing these cranes, including annual load tests at 110% of rated capacity. Compliance ensures that cranes remain safe and operational, even in the harsh conditions of a mine.
SANS 10295-1 and SANS 10295-5: Safety Rules for Electric Lifts and Goods-Only Lifts
These standards govern the design, construction, and installation of electric lifts (SANS 10295-1) and electric/hydraulic goods-only lifts (SANS 10295-5). In mines, lifts are used to transport workers and materials vertically through shafts. These standards ensure that lifts meet stringent safety requirements, including electrical and mechanical integrity, to prevent accidents.
Addressing Common Questions
You might be wondering, “Which standard is the most important?” The answer depends on the equipment. For hoists, SANS 1594 and SANS 1636 are critical for manual operations, while SANS 2408 and SANS ISO 4309 are key for wire rope-based systems. For lifts, SANS 10295-1 and -5 are non-negotiable. Each standard addresses a specific component or process, working together to create a safe lifting ecosystem.
Benefits of SANS Compliance
Compliance with SANS standards offers tangible benefits for South African mines, from safety to cost savings. Here’s how:
Enhanced Safety
The primary goal of SANS standards is to protect workers. By specifying robust materials, precise designs, and regular maintenance, these standards reduce the risk of equipment failures that could lead to accidents. For example, SANS ISO 4309’s discard criteria for wire ropes prevent sudden failures, while SANS 1594 ensures chain blocks can handle heavy loads without breaking.
Improved Reliability
SANS-compliant equipment is designed to withstand the harsh conditions of mining, such as dust, moisture, and extreme temperatures. This reliability translates to fewer breakdowns, ensuring that hoists and cranes keep operations running smoothly. For instance, SANS 2408-compliant wire ropes are tested for fatigue resistance, reducing the likelihood of unexpected downtime.
Cost Savings
While SANS compliance requires investment in quality equipment and regular inspections, it saves money in the long run. Fewer accidents mean lower medical and compensation costs, while reliable equipment reduces repair and replacement expenses. For example, adhering to SANS 0019’s inspection protocols for mobile cranes can extend their service life, saving mines thousands of rands.
Regulatory Compliance
The Mine Health and Safety Act mandates that lifting equipment meet appropriate standards, with SANS being the benchmark. Non-compliance can result in fines, shutdowns, or legal liability. By following SANS standards, mines avoid penalties and demonstrate a commitment to safety, which is critical for maintaining a good reputation in the industry.
Common Concerns Addressed
Some mine operators worry that SANS compliance is too costly or complex. However, the long-term benefits far outweigh the initial effort. Investing in SANS-compliant equipment and training competent inspectors ensures that mines operate safely and efficiently, protecting both workers and profits.
Why It Matters to South Africans
Mining is more than an industry in South Africa—it’s a way of life for many communities. From the gold mines of Gauteng to the platinum fields of Rustenburg, the sector employs thousands and supports entire towns. But with great economic impact comes great responsibility. Unsafe equipment can lead to tragic accidents, devastating families and disrupting livelihoods. SANS standards are a critical tool in preventing such outcomes.
For South Africans, SANS compliance means safer workplaces. Miners can go underground knowing that the hoists and lifts they rely on meet rigorous safety standards. Mine managers benefit from reduced downtime and compliance with the Mine Health and Safety Act, which requires lifting equipment to be inspected every three months and load-tested annually by a registered LMI. Communities near mines also benefit, as safer operations reduce the risk of environmental or economic disruptions caused by accidents.
Moreover, SANS standards align with South Africa’s commitment to global best practices. By adopting standards like SANS ISO 4309 and SANS ISO 8539, the country ensures that its mining industry remains competitive on the world stage. This is crucial for attracting investment and maintaining South Africa’s position as a leading mineral producer.
For those asking, “How do I ensure my mine is SANS-compliant?” the answer lies in working with reputable suppliers, training staff, and scheduling regular inspections. The SABS website (www.sabs.co.za) provides access to standard documents, while registered LMIs can assist with compliance checks.
Conclusion
South African mines operate in some of the toughest conditions on Earth, and hoists and lifting equipment are critical to their success. The South African National Standards (SANS), set by the SABS, provide a robust framework for ensuring that this equipment is safe, reliable, and fit for purpose. Standards like SANS 1594, SANS 2408, SANS ISO 4309, and SANS 10295-1 cover every aspect of lifting systems, from chain blocks to wire ropes to electric lifts. By adhering to these standards, mines reduce accidents, improve equipment reliability, and comply with the Mine Health and Safety Act.
For South Africans, SANS compliance is more than a regulatory requirement—it’s a commitment to protecting workers and sustaining the mining industry. Whether you’re a miner, manager, or supplier, understanding and implementing these standards is essential for safer, more efficient operations. Visit the SABS website or consult a registered Lifting Machinery Inspector to ensure your equipment meets SANS requirements. In a country where mining powers progress, SANS standards are the foundation of a safer future.
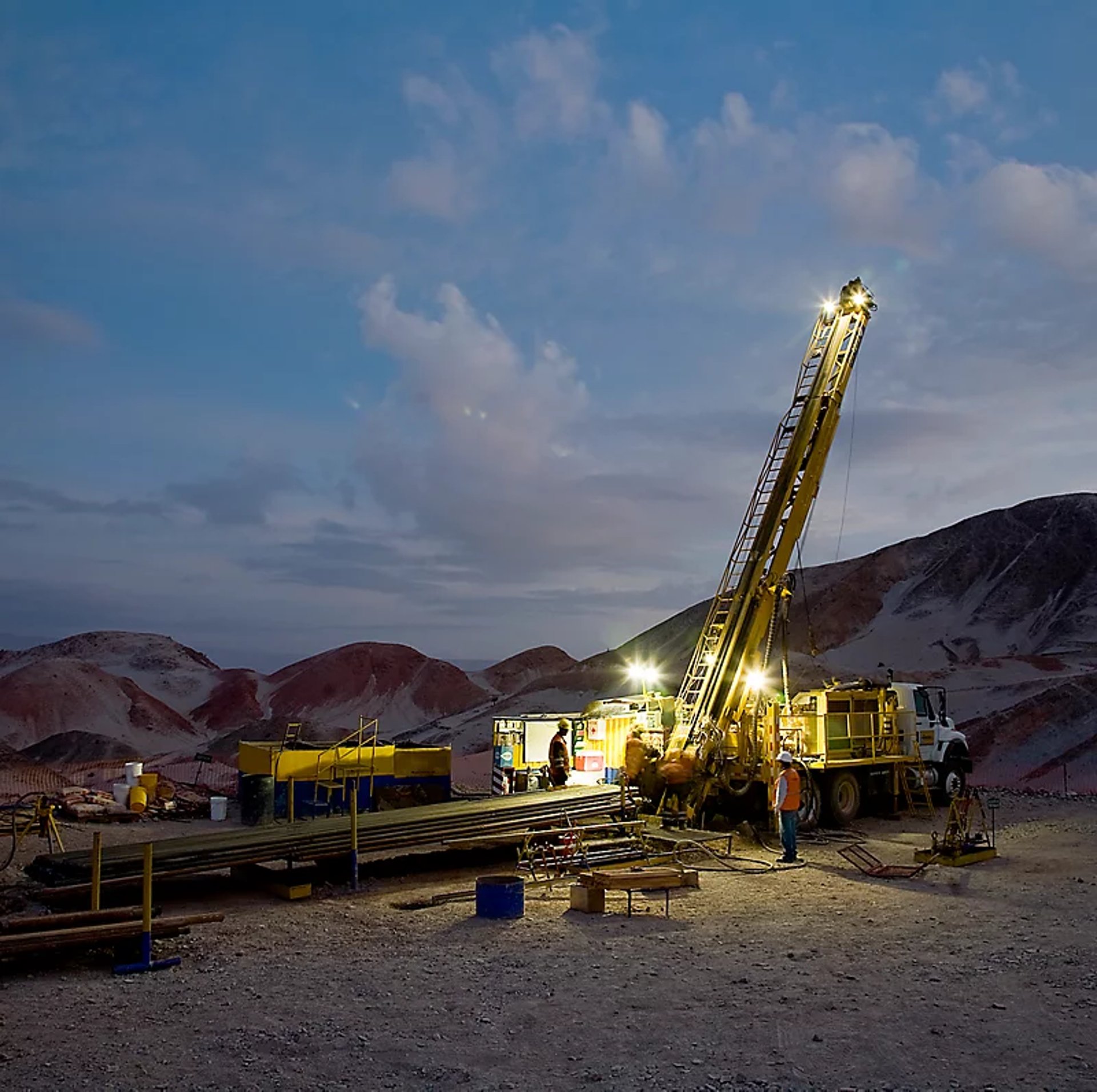
Feichun Mining Cables
Durable mining cables for harsh environments and operations.
Email Address: Li.wang@feichuncables.com
© 2025. All rights reserved.
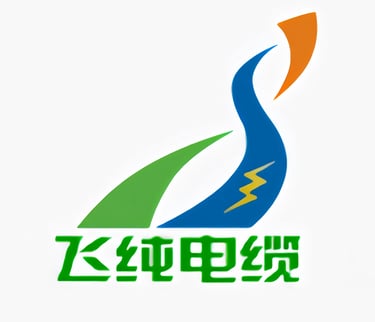
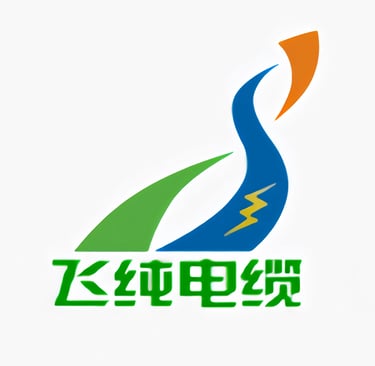
One-click to Quickly Contact