Anhui Feichun Special Cable Co.,Ltd Li.wang@feichuncables.com
Why Are Trailing Cables Essential for South Africa's Mining and Heavy Industries?
South Africa's mining sector stands as one of the world's most demanding industrial environments, where reliable power distribution can mean the difference between operational success and costly downtime. At the heart of this power infrastructure lie trailing cables – specialised electrical conductors designed to deliver power to mobile equipment across challenging terrains and harsh conditions.
Li.wang@Feichun Cable
7/9/202510 min read
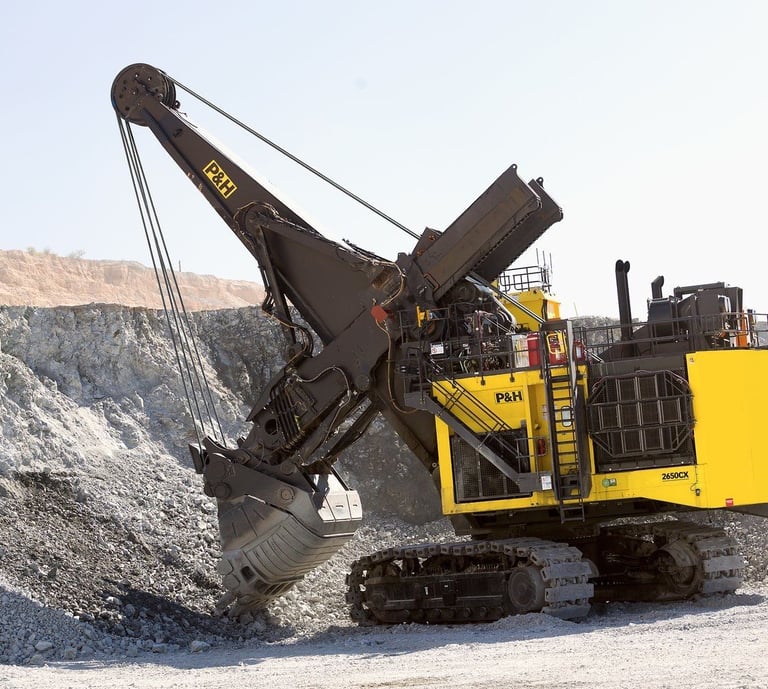
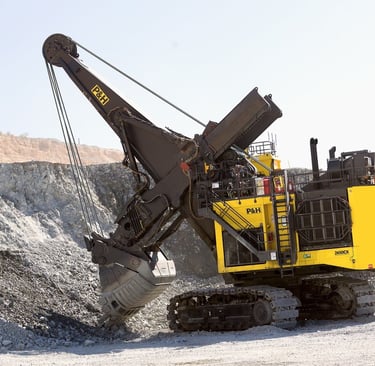
Introduction
Trailing cables represent a critical component in South Africa's mining and heavy industrial landscape, serving as the lifeline that connects stationary power sources to mobile equipment operating in dynamic environments. These robust electrical conductors are engineered to withstand the extreme conditions found in mines, construction sites, and industrial facilities across the country.
The importance of trailing cables in South Africa's mining and industrial sectors cannot be overstated. With the country's mining industry contributing significantly to the national economy and employing hundreds of thousands of workers, the reliability and safety of power distribution systems directly impact productivity, worker safety, and operational continuity. From the gold mines of the Witwatersrand to the platinum operations in the Bushveld Complex, trailing cables ensure that draglines, shovels, conveyors, and other mobile equipment receive consistent power supply despite constant movement and harsh environmental conditions.
Design and Characteristics of Trailing Cables
Construction and Materials
Trailing cables designed for South African mining applications incorporate sophisticated construction techniques that address the unique challenges of the local environment. The typical construction consists of multiple copper conductors surrounded by high-grade insulation materials, protective sheathing, and reinforcement elements designed to withstand mechanical stress.
The conductor cores are typically made from high-purity copper, chosen for its excellent electrical conductivity and resistance to corrosion – particularly important in South Africa's varied climate conditions. The insulation system often employs cross-linked polyethylene (XLPE) or ethylene propylene rubber (EPR), materials that maintain their properties across wide temperature ranges and resist degradation from moisture, chemicals, and ultraviolet radiation.
The outer sheath incorporates specialised compounds that resist oil, flame, and abrasion – essential properties for equipment operating in mining environments where exposure to hydraulic fluids, fuel, and rough surfaces is constant. Many cables designed for South African applications also include additional protective layers such as steel wire armouring or textile braiding to enhance mechanical protection.
Flexibility and Durability
One of the most critical characteristics of trailing cables is their ability to maintain flexibility while providing exceptional durability. This balance is achieved through careful selection of materials and construction techniques that allow the cable to bend, twist, and flex repeatedly without compromising electrical integrity or mechanical strength.
The cable design incorporates stranded conductors rather than solid wire, enabling better flexibility and reducing stress concentration during movement. The insulation and sheathing materials are formulated to remain pliable across the temperature ranges commonly encountered in South African mining operations, from the cool depths of underground mines to the intense heat of surface operations in summer.
Durability testing for these cables often exceeds international standards, with manufacturers conducting accelerated aging tests, repeated flex testing, and exposure to harsh chemicals and environmental conditions that simulate decades of use in South African mining conditions.
Safety Features
Safety remains paramount in trailing cable design, with multiple features incorporated to protect both equipment and personnel. Flame-retardant materials are standard, meeting strict fire safety requirements that are particularly important in underground mining environments where escape routes may be limited.
Ground fault protection is built into the cable design through dedicated grounding conductors that provide multiple paths for fault current, ensuring rapid detection and isolation of electrical faults. This feature is crucial in South Africa's mining operations where worker safety regulations are strictly enforced and electrical accidents can have severe consequences.
Many trailing cables also incorporate pilot conductors that enable remote monitoring of cable condition, allowing operators to detect potential issues before they result in failures. This predictive maintenance capability is increasingly valuable in South African mining operations where equipment downtime can be extremely costly.
Applications of Trailing Cables in South Africa
Mining Industry
The mining sector represents the largest application area for trailing cables in South Africa, with these specialised conductors powering a wide range of mobile equipment across various mining operations. In underground mines, trailing cables connect stationary power distribution points to continuous miners, shuttle cars, roof bolters, and other mobile equipment that must move freely throughout the mine workings.
Surface mining operations, including the massive open-pit mines found in South Africa's mineral-rich regions, rely on trailing cables to power draglines, electric shovels, and other large-scale earth-moving equipment. These applications demand cables capable of carrying extremely high currents – often thousands of amperes – while withstanding constant movement across rough terrain.
Coal mining operations in Mpumalanga province extensively use trailing cables for longwall systems, where the cables must follow the cutting equipment as it advances through the coal seam. The cables must be designed to handle not only the electrical demands but also the mechanical stresses associated with constant repositioning and the harsh underground environment.
Gold mining operations in the Witwatersrand region utilise trailing cables for underground transportation systems, ventilation equipment, and mobile mining machinery. The deep nature of these mines presents unique challenges, including high temperatures, humidity, and the need for cables that can operate reliably at significant depths.
Construction and Heavy Industries
South Africa's construction industry relies heavily on trailing cables for powering mobile equipment at construction sites, particularly for large infrastructure projects such as road construction, building developments, and industrial facility construction. These applications require cables that can withstand outdoor exposure to South Africa's varied weather conditions while providing reliable power to cranes, concrete pumps, and other construction equipment.
The petrochemical industry, centred in areas like Secunda and Sasolburg, uses trailing cables for mobile equipment in refineries and chemical processing facilities. These applications demand cables with enhanced chemical resistance and special safety features to handle the hazardous environment.
Manufacturing facilities across South Africa employ trailing cables for automated guided vehicles, mobile robots, and other equipment that requires power while moving throughout the facility. The automotive industry, particularly in the Gauteng province, uses these cables extensively for assembly line equipment and material handling systems.
Port and Industrial Automation
South Africa's major ports, including Durban, Cape Town, and Richards Bay, rely on trailing cables for powering mobile equipment such as container cranes, ship-to-shore cranes, and automated guided vehicles used in cargo handling operations. These marine environments present unique challenges, including salt spray, high humidity, and the need for cables that can operate reliably in coastal conditions.
Industrial automation systems in manufacturing facilities use trailing cables to power robotic systems, automated storage and retrieval systems, and other equipment that requires mobility while maintaining electrical connections. The increasing automation in South African industries has driven demand for more sophisticated trailing cable solutions that can handle both power and data transmission.
Why South Africa's Harsh Mining Conditions Demand Trailing Cables
Geological and Environmental Challenges
South Africa's mining operations face some of the world's most challenging geological and environmental conditions, making the selection and design of trailing cables particularly critical. The country's deep underground mines, some extending more than 3,000 metres below surface, present extreme conditions including high temperatures, humidity, and rock pressure that can impact cable performance.
The geological diversity across South Africa's mining regions creates varied challenges for cable systems. Hard rock mining operations in areas like the Bushveld Complex require cables that can withstand abrasion from sharp rock surfaces and dust containing silica and other abrasive materials. Softer rock formations in coal mining regions present different challenges, including potential exposure to methane gas and the need for intrinsically safe electrical systems.
Surface mining operations must contend with South Africa's extreme weather variations, from intense summer heat exceeding 40°C to winter conditions that can include frost and occasional snow in higher elevations. The cables must maintain their electrical and mechanical properties across these temperature extremes while resisting degradation from ultraviolet radiation.
The presence of corrosive substances in many South African mining environments, including acid mine drainage and various chemical processing byproducts, requires cables with enhanced chemical resistance. This is particularly important in operations such as platinum mining, where exposure to various acids and processing chemicals is common.
Compliance with Local Standards
South Africa's mining industry operates under strict regulatory frameworks that mandate specific requirements for electrical equipment, including trailing cables. The Mine Health and Safety Act and associated regulations establish comprehensive requirements for electrical systems in mining operations, with specific provisions for mobile equipment and trailing cable installations.
The South African Bureau of Standards (SABS) has developed specific standards for mining cables, including SANS 1507 which covers requirements for flexible cables used in mining applications. These standards address construction requirements, testing procedures, and performance criteria that ensure cables can operate safely and reliably in South African mining conditions.
The National Regulator for Compulsory Specifications (NRCS) requires that all electrical equipment used in mining operations meet specific safety and performance standards. This includes comprehensive testing and certification procedures that verify cable performance under conditions representative of South African mining environments.
Compliance with these local standards is not merely a regulatory requirement but a practical necessity, as the standards have been developed based on the specific challenges and conditions encountered in South African mining operations. Cables that meet these standards are more likely to provide reliable service and contribute to safe mining operations.
Potential Challenges and FAQs
Common Issues with Trailing Cables
Despite their robust design, trailing cables in South African mining operations can face several challenges that impact their performance and longevity. Mechanical damage remains one of the most common issues, often resulting from contact with sharp objects, crushing by heavy equipment, or excessive bending beyond the cable's minimum bend radius.
Electrical failures can occur due to moisture ingress, particularly in underground operations where humidity levels may be high or where cables are exposed to water from mining processes. Insulation degradation over time can lead to ground faults or short circuits, potentially causing equipment damage or safety hazards.
Corrosion of conductor materials can occur in environments with high acidity or the presence of corrosive chemicals. This is particularly relevant in certain South African mining operations where acid mine drainage or chemical processing creates challenging conditions for electrical equipment.
Thermal cycling, where cables are subjected to repeated heating and cooling cycles, can cause materials to expand and contract, potentially leading to mechanical stress and eventual failure. This is particularly relevant in applications where cables are exposed to varying ambient temperatures or where electrical loading varies significantly.
Frequently Asked Questions
How long do trailing cables last in South African mines?
The lifespan of trailing cables in South African mining operations depends on several factors including usage patterns, environmental conditions, and maintenance practices. Under typical conditions, high-quality trailing cables designed for mining applications can last between 5 to 15 years, with some installations exceeding 20 years with proper maintenance.
Usage intensity plays a crucial role in determining cable life. Cables used in continuous operations with frequent movement will typically have shorter lifespans than those used intermittently. The type of equipment and the nature of its movement also impact longevity – cables serving equipment with predictable, gentle movements typically last longer than those subjected to harsh, erratic movements.
Environmental factors specific to South African mining operations significantly influence cable life. Underground operations with controlled environments may provide longer cable life compared to surface operations exposed to extreme weather conditions. However, underground operations with high humidity, temperature, or chemical exposure may reduce cable life.
Regular maintenance and inspection programmes can significantly extend cable life. This includes visual inspections for signs of wear or damage, electrical testing to verify insulation integrity, and proper cable handling and storage practices. Many South African mining operations have implemented predictive maintenance programmes that monitor cable condition and replace cables before failure occurs.
Can trailing cables be used in both underground and surface mining?
Yes, trailing cables are versatile and suitable for both underground and surface mining applications, though specific design modifications are often necessary for each environment. The fundamental construction principles remain the same, but the emphasis on certain characteristics may vary based on the specific application.
Underground mining applications typically require cables with enhanced flame retardancy and low smoke emission characteristics to meet safety requirements for enclosed spaces. The cables may also need to be designed for operation in higher humidity environments and may require additional protection against chemical exposure from mining processes.
Surface mining applications often emphasise weather resistance, particularly protection against ultraviolet radiation, extreme temperatures, and moisture from rain or snow. The cables may need enhanced mechanical protection to withstand the harsh conditions of open-pit mining operations.
Many manufacturers offer cable designs that are suitable for both applications, providing flexibility for mining operations that use equipment in both underground and surface applications. However, it's important to verify that the specific cable design meets the requirements for the intended application environment.
What should I look for when selecting trailing cables for my mining operation?
When selecting trailing cables for South African mining operations, several key factors should be considered to ensure optimal performance and safety. First and foremost, verify that the cables meet relevant SANS and NRCS standards, as compliance with these standards is essential for regulatory approval and operational safety.
Look for cables with proven resistance to abrasion, moisture, and temperature fluctuations that are characteristic of South African mining environments. The cable should be designed to withstand the specific mechanical stresses of your application, including the types of movement, bend radius requirements, and potential exposure to crushing forces.
Consider the electrical requirements of your application, including voltage levels, current carrying capacity, and any special requirements such as intrinsic safety for hazardous locations. Ensure that the cable design includes appropriate safety features such as ground fault protection and flame retardancy.
Evaluate the manufacturer's experience and reputation in the South African mining market, as local knowledge and support can be crucial for successful cable selection and ongoing support. Consider factors such as availability of spare parts, technical support, and the manufacturer's understanding of local operating conditions.
Finally, consider the total cost of ownership, including not just the initial purchase price but also factors such as expected lifespan, maintenance requirements, and potential downtime costs. A higher-quality cable with longer life and better reliability may provide better value despite a higher initial cost.
Conclusion
The Growing Demand for Reliable Power Systems
The future of South Africa's mining and heavy industries increasingly depends on reliable, efficient power distribution systems that can adapt to evolving operational requirements and environmental challenges. Trailing cables will continue to play a crucial role in this landscape, serving as the vital link between stationary power sources and mobile equipment across diverse industrial applications.
As South African mining operations become more mechanised and automated, the demands on trailing cable systems will continue to increase. The need for cables that can handle higher power levels, incorporate data transmission capabilities, and provide enhanced monitoring and diagnostic features will drive continued innovation in cable design and manufacturing.
The growing emphasis on sustainability and environmental responsibility in South African mining operations will also influence trailing cable development. This includes the development of cables with longer lifespans, improved recyclability, and reduced environmental impact during manufacturing and disposal.
Future trends in cable technology point toward enhanced durability and environmental resilience through the incorporation of advanced materials and construction techniques. Smart cable systems that can provide real-time monitoring of their condition and performance will become increasingly common, enabling predictive maintenance strategies that improve reliability and reduce operational costs.
The integration of renewable energy sources into mining operations presents new challenges and opportunities for trailing cable systems. As solar and wind power become more prevalent in South African mining operations, trailing cables will need to be designed to handle the variable power characteristics of these sources while maintaining the reliability required for critical mining operations.
In conclusion, trailing cables remain an essential component of South Africa's mining and heavy industrial infrastructure, enabling safe and efficient operations in some of the world's most demanding environments. Their continued evolution and improvement will be crucial to supporting the country's mining sector as it adapts to changing economic, environmental, and technological challenges. The investment in high-quality trailing cable systems represents not just a technical necessity but a strategic decision that impacts operational efficiency, worker safety, and long-term sustainability of South Africa's vital mining industry.
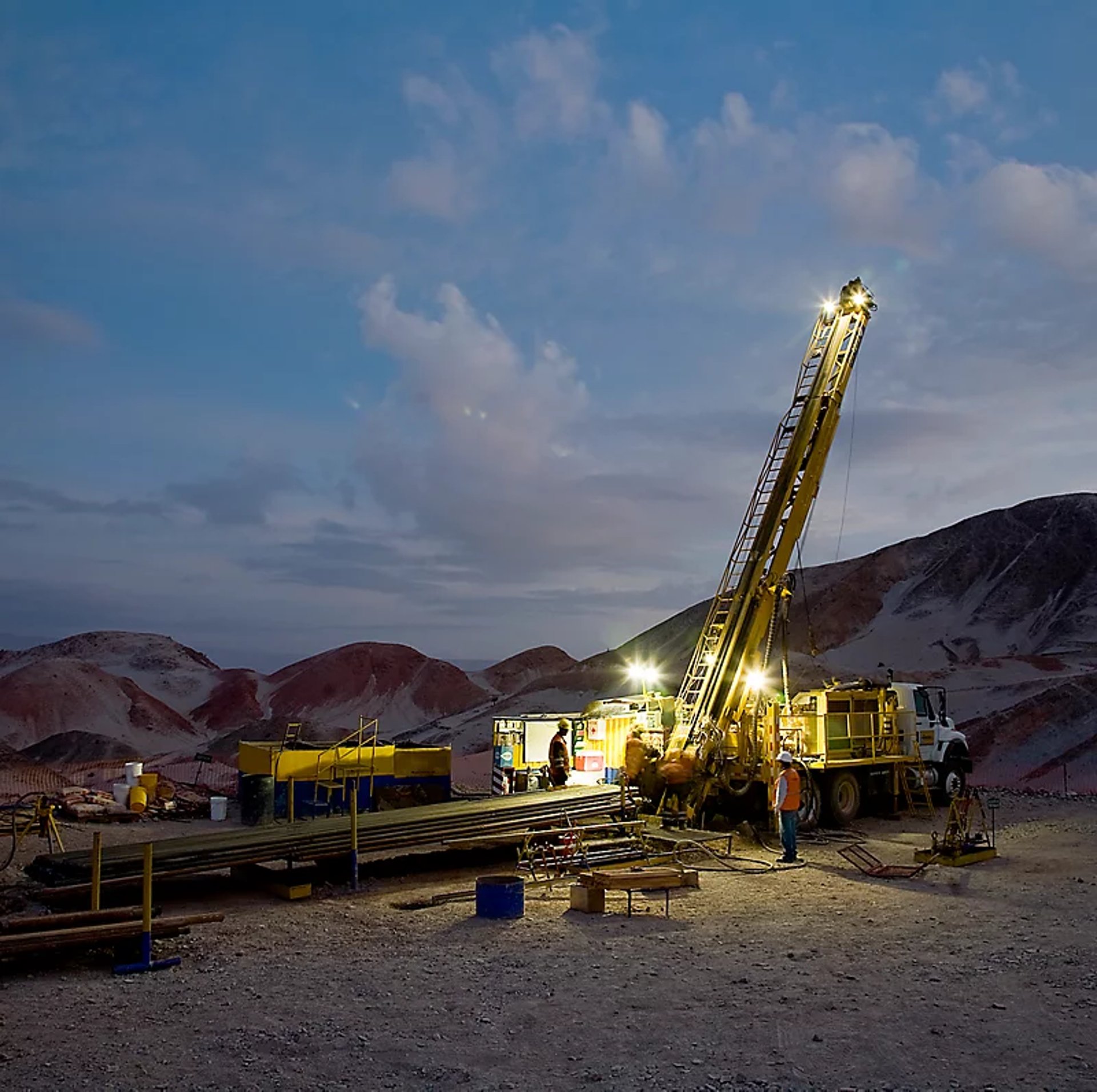
Feichun Mining Cables
Durable mining cables for harsh environments and operations.
Email Address: Li.wang@feichuncables.com
© 2025. All rights reserved.
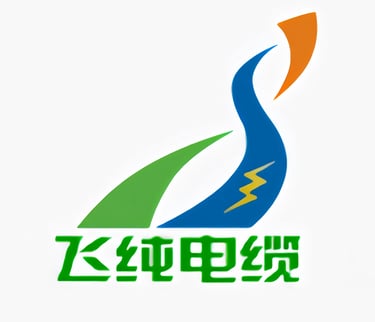
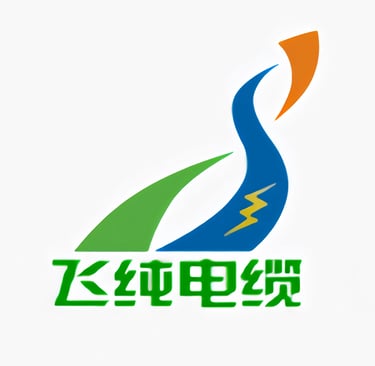
One-click to Quickly Contact